A method to look at subsurface cracks and their growth patterns to determine topographical characteristics of material fatigue
The 75 Years of Innovation series highlights the groundbreaking innovations spanning from SRI’s founding in 1946 to today. Each week, SRI will release an innovation, leading up to its 75th anniversary in November 2021.
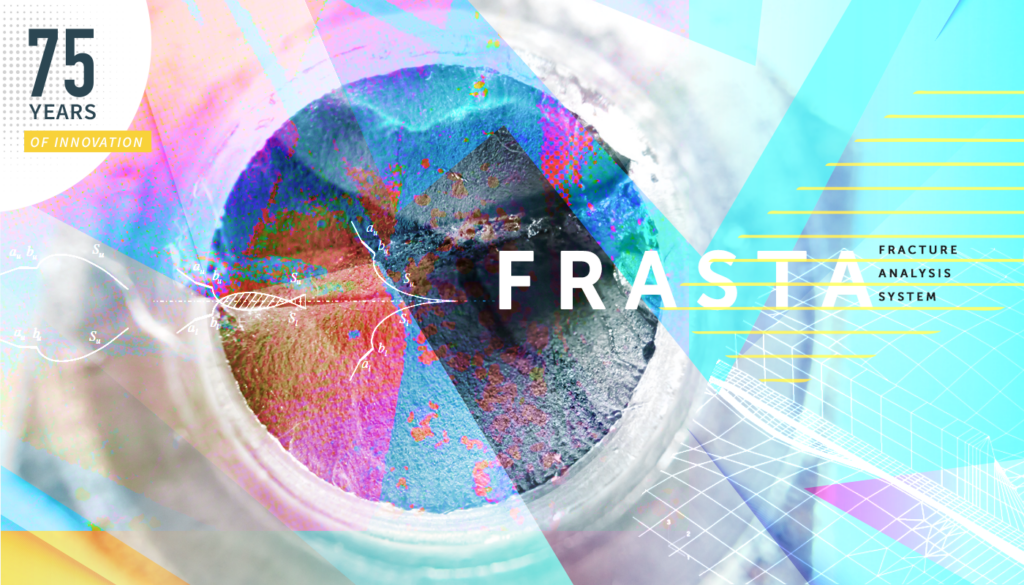
Looking for Trouble: How SRI’s Fracture Analysis System (FRASTA) Helps to Save Lives
Metals and other more recent materials such as plastics, have created the modern world we know today. These materials are integral to how we live, work, and travel. When these materials fail it can have disastrous results.
In the 1980s, SRI International developed a technology system to quantify and interpret material fatigue using fracture surface topography. This system, FRASTA (FRacture Surface Topography Analysis), provides a mechanism to reconstruct a fracture event, providing details of the fracture history, trajectory and even possible causes, to help prevent failure in materials such as metal.
The Material Culture of FRASTA
Engineers are always looking for ways to optimize their inventions. To do so, they have to look at the materials they use. Material scientists are masters of ‘stuff’, understanding the structural details of the materials used to build everything from bridges to coffee machines to airplanes. Metals are used in the fabrication of a plethora of objects, and crude steel production in the first 6-months of 2018 was1,036 million tons. In other words, we use a lot of metal. But like every material, metal has its flaws.
By analyzing details of a fractured surface, material scientists can help to understand the cause of failure in a product. If you can understand material flaws, how they are created, and how they develop, you can use that knowledge to optimize your use of a particular material. FRASTA was developed as a method to reconstruct the 3-dimensional history of a fracture process to provide an understanding of the micromechanics of failure. By providing this data to engineers and material scientists, structures can be improved. An example of this could be applying FRASTA data to develop lighter yet structurally stronger airplane parts.
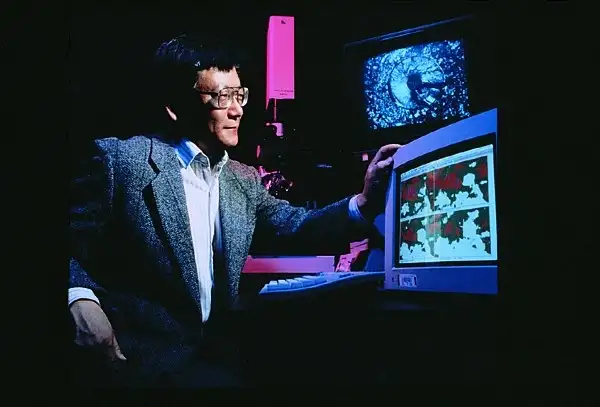
How FRASTA Helps to Prevent Failure
FRASTA is based on a ‘fractographic’ technique that can be applied within the discipline of ‘fractography’, or Fracture Surface Topography Analysis. It uses both hardware and software to carry out the analysis of a material fracture.
FRASTA works by using a confocal optics scanning laser microscope to look at the material. This laser microscope provides high-resolution optical imaging enhanced with depth selectivity to provide optical sectioning of the material object.
The resulting images are a topography of the conjugate fracture surface shown at different depths of the material. A number of these images are taken, then superimposed and compared using FRASTA software to build up a picture of the fracture process. This comparison allows engineers to observe how the fracture surface increases across conjugate fracture surfaces.
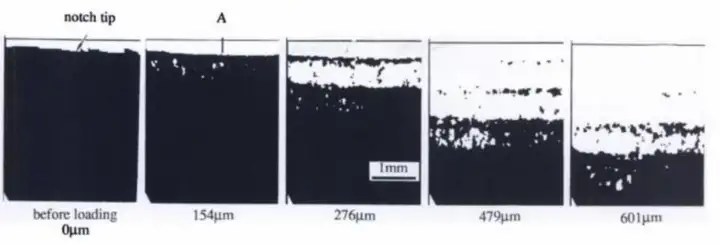
FRASTA Looking Beneath the Surface for Cracks
FRASTA is a breakthrough technology that provides the tools to allow engineers and scientists to understand how and why structures fail. FRASTA is used to understand the dynamics of material failure, including metal fatigue. These data can be used to predict fatigue failure in everyday commercial objects including, aircraft, bridges, and pipelines.
Understanding the microstructure of a material and how those features affect a fracture is important in engineering projects. Understanding how fracture events happen and the impact of a particular structure on a fracture provides information to make a material more efficient and effective for an engineering task.
FRASTA has helped companies including NASA, Mitsubishi Heavy Industries, Osaka Gas Company, and Chubu Electric Power Company to see inside a material to look at what lies beneath the surface; to see how cracks form and what happens to those cracks over time. By creating precise topographic maps of a material, FRASTA provides a visual statement of what happens below the surface of a material. The intelligence provided by this process can inform engineers and material scientists about the factors that make materials, such as metal, fail.
Using the knowledge provided by FRASTA, on material fatigue, structures can be optimized, costs-reduced, efficiency improved and ultimately, lives saved.
Interested to see more from SRI?
Visit sri.com.
Resources
Donald Shockeyand Takao Tobayashi, The Second Joint NASA/FAA/DoD Conference on Aging Aircraft, 1999: https://ntrs.nasa.gov/archive/nasa/casi.ntrs.nasa.gov/19990049248.pdf
Kobayashi, Takao and Shockey, Donald, 2010/08/01, Fracture surface topography analysis (FRASTA) — Development, accomplishments, and future applications, Engineering Fracture Mechanics: https://www.researchgate.net/publication/223655315_Fracture_surface_topography_analysis_FRASTA-Development_accomplishments_and_future_applications
Deloitte, Overview of Steel and Ore Market: https://www2.deloitte.com/content/dam/Deloitte/ru/Documents/energy-resources/overview-of-the-steel-and-iron-market-en.pdf
T. Kobayashi and D. A. Shockey, “FRASTA: A New Way to Analyze Fracture Surfaces, Part 1: Reconstructing Crack Histories,” Advanced Materials & Processes, Vol. 140, pp.28–34 (1991)
Derek Hull, Fractography: Observing, Measuring and Interpreting Fracture Surface Topography, Cambridge University Press, 1999 ISBN 0521646847, 9780521646840