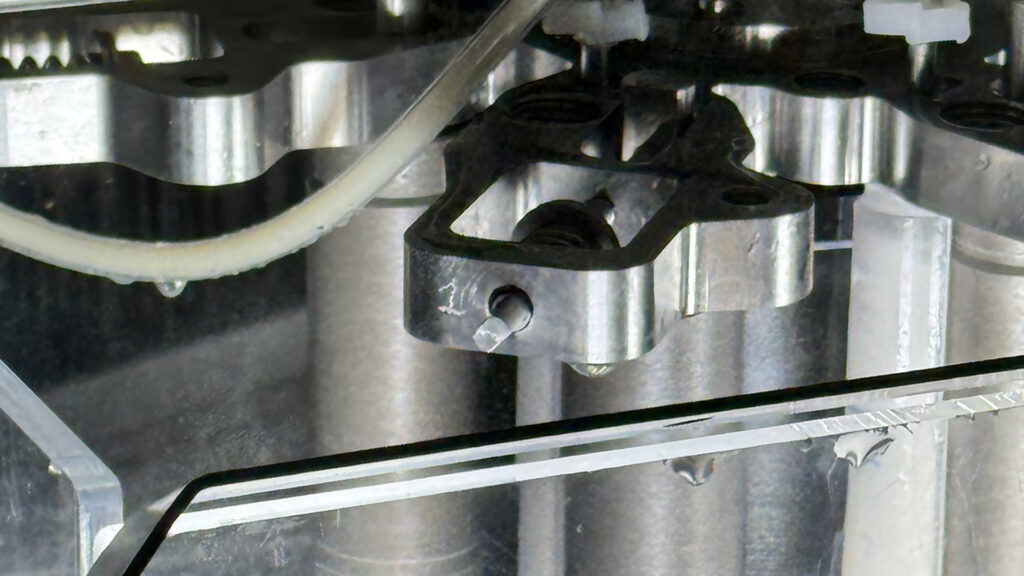
A new spray-drying technology could cut high energy costs and increase efficiency across large industries.
Across food, chemical, pharmaceutical, and other industries, many liquid materials are turned into fine powders through spray drying for use in tablets, powders, capsules, paints, or dried foods.
The problem, however, is that today’s methods of drying using nozzles require a lot of energy and don’t work when the manufacturers want to dry thick or viscous materials. “Existing technologies are limited when spraying thick and viscous materials, especially if they contain 50 percent water or less,” said David Johnson, associate director of the mechanical and fluid systems group at SRI. “Evaporating water from thick materials requires an enormous amount of energy.”
Lowering carbon emissions
A new technology from SRI allows manufacturers to spray difficult materials while dramatically cutting energy costs. SRI’s Filament Extension Atomizer (FEA) uses rollers instead of nozzles to spray materials, reduces the energy consumption of spray drying by 40 percent, and could potentially eliminate 1.5 million tons of carbon dioxide emissions annually across the food, chemical, and pharmaceutical industries.
It works by squeezing fluid between two high-speed rollers in contact with each other, which spin to create filaments and stretch them to their breaking point until they fracture into fine droplets. By varying the process settings of the system (like roller size or speed), researchers can produce different-sized droplets for a variety of applications.
“A new technology from SRI allows manufacturers to spray difficult materials while dramatically cutting energy costs.” – David Johnson
The team has demonstrated that FEA spray technology can save time and energy, especially when drying thick or viscous liquids. And, many difficult-to-spray materials exhibit a property called extensional hardening, which causes them to form long filaments when they are put under strain. Operating differently from existing spray methods, FEA takes advantage of this property instead of trying to fight it.
Saving money and reducing waste
Potential uses for FEA include drying various polymers, thermoplastics, paints, coatings, a wide range of food products, cosmetics, medicine, and therapeutics. The technology could also enable next-gen spray-on consumer products. A hand-held version could be used to spray thick sunscreen or cosmetics easily. This would offer benefits including lower shipping costs, convenient packaging, and less waste. Similarly, FEA could be used for environmentally friendly spray-on paints or coatings using fewer solvents.
There are other applications in the dairy industry, which use spray drying to turn whey, a byproduct of cheese and yogurt, into protein-rich powders. Today, whey needs to contain more than 50 percent water to be spray-dried. SRI researchers have shown that FEA can spray whey materials that contain only 20 percent water. “Our technology greatly reduces the amount of water needed. In large-scale industrial applications, that translates into significant energy savings and carbon reductions,” said Johnson.
SRI is currently working with the U.S. Department of Energy (DOE) and industrial partners to mature this technology and help manufacturers realize savings across the U.S. Food and Beverage industry. “FEA offers a new and different way of making products inspired by the natural behavior of fluids,” Johnson said. “On their own, certain fluids make filaments and break into droplets. We’ve found a way to take advantage of these properties to produce a fine spray that requires very little energy.”
This material is based upon work supported by the U.S. Department of Energy’s Office of Energy Efficiency and Renewable Energy (EERE) under the Advanced Manufacturing Office Award Number DE-EE0009128. The views expressed herein do not necessarily represent the views of the U.S. Department of Energy or the United States Government