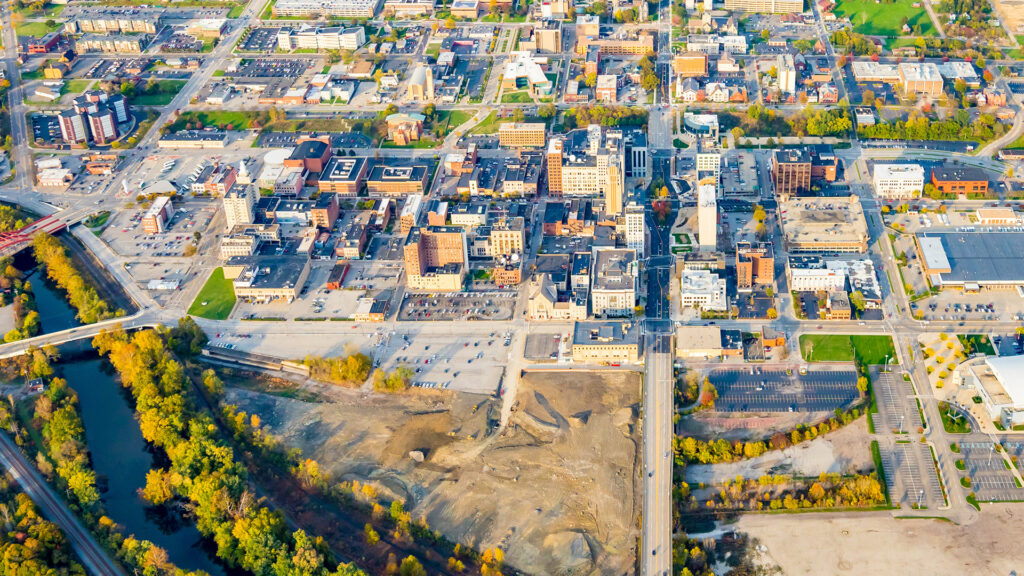
A new SRI study examines the readiness of a historic manufacturing base to support the transition to EV battery manufacturing.
Promising that half of all cars made in the U.S. by 2030 will be zero-emission vehicles, the Biden-Harris Administration has inspired high hopes in the American manufacturing sector. But, at a time of record employment, many industry watchers worry there won’t be enough skilled labor to fill the expected jobs. In that light, policy experts have pointed to the legendary manufacturing region of Northeastern Ohio as a seemingly natural new home for American electric vehicle (EV) battery makers, with an experienced and ready labor force. The question turns to whether those workers will have the skills needed to succeed in the advanced battery manufacturing facilities.
To answer that question, a team of analysts from SRI’s Center for Innovation Strategy and Policy (CISP) recently published an in-depth, multi-dimensional study of the Ohio cities of Youngstown, Warren, and Boardman metropolitan statistical area — a region dubbed “Voltage Valley.” These towns, once famous for making steel and vehicles, could make an attractive new home for American EV battery makers, but there are meaningful challenges to making it happen.
“Given the scale of collaboration in the region between industry, policymakers, and workforce partners, we assumed the answer to the question of workforce readiness would be ‘yes,’” said study co-author Christiana McFarland, director of CISP at SRI. “But it’s not a slam dunk. Our study identifies the inherent strengths of Northeastern Ohio’s EV battery manufacturing workforce and points out notable gaps that will need to be filled to ensure success in the region.” These gaps stem largely from the push to revolutionize the manufacturing sector with the digital transformation of manufacturing and the development of advanced engineering technologies required for making EV batteries.
Nuanced analysis
The team used mixed methods, including supply-and-demand analysis and analysis of National Labor Exchange job posting data to identify the most desirable skills that EV battery makers are looking for. They mapped those skills to the curriculum at local trade and high schools and community colleges. In addition, conducting first-person interviews with regional stakeholders helped to refine their analysis.
The study noted that the Youngstown-Warren-Boardman community is already the number one auto parts producer in the U.S. and second only to Michigan in assembling cars. Despite this distinction, the manufacturing infrastructure and the technical skills needed to make EV batteries are not adequate. The analysis found that regional demand for EV battery manufacturing workers outpaces supply nearly two to one. This undersupply even accounts for workers in other industries with skills that are compatible with, or transferrable to, EV battery manufacturing.
“We find that most skills demanded by EV battery manufacturing employers are typical of many manufacturing environments, but that EV battery manufacturing also requires highly specialized technical skills, such as chemical process safety and the maintenance and operation of industrial robots,” said McFarland. “This underscores the opportunity for workers in other manufacturing jobs to shift to EV battery manufacturing, but also the important role of employers to train new hires with on-the-job processes specific to EV battery manufacturing.”
Recommended steps
The authors detail recommendations for policymakers in the Youngstown region, and any potential EV battery manufacturing region, to consider as they work to attract EV battery companies and ensure workers are prepared to meet demand. Among them, regional leaders must build strong partnerships between industry and local community colleges and trade schools to develop appropriate curriculum, expand apprenticeship programs to get young people involved as early as possible, and improve marketing efforts to attract talent to the region.
And the region already has a head start. For example, Cuyahoga Community College and Eastern Gateway Community College offer several programs that support skills development directly related to EV battery manufacturing, particularly Operations Engineering Technology, Industrial Maintenance Technology, Smart Manufacturing–Mechatronics, and Machining programs.
“Our study identifies the inherent strengths of Northeastern Ohio’s EV battery manufacturing workforce.” — Christiana McFarland
Regional employers also recognize their role in attracting new workers to the industry and developing the skills needed in an EV battery manufacturing environment. For example, Ultium Cells, an EV battery manufacturing joint venture between GM and LG Energy Solutions, hosted students for battery cell demonstrations that are made at the plant. Meanwhile, GM invested $5 million at a local state university to develop workforce training. Foxconn, the company best known for making iPhones, partnered with that same university to form an EV training and innovation center to help prepare students to work in its Lordstown, Ohio, EV facility.
Despite these efforts, the region is still struggling to fill EV battery manufacturing roles. Regional leaders can also look to existing state programs and advocate for them to be available to the region and for EV battery manufacturing. For example, Ohio TechNet’s TRAIN OH can be scaled to engage EV battery manufacturers. TRAIN OH is a robust earn-and-learn upskilling program where companies and educators integrate activities supported by a network of education, government, and industry institutions. Additionally, the state is already making significant K–12 engagement efforts through the DriveOhio initiative. The initiative provides grant funding to improve access to STEM technologies in classrooms but is only available to a limited number of schools and excludes schools in the Youngstown region. Advocating for expanded access to these grant funds will support the region’s K–12 institutions in its capacity to build meaningful career pathways into EV battery manufacturing roles.
“In many ways, the region is ahead of the curve but faces challenges quickly building a workforce aligned with advanced manufacturing, energy storage, and other integrated technology solutions,” said McFarland. “Scaling what works and doubling down on the resources, commitment, and collaboration needed to meet demand will ensure a strong future in Northeast Ohio.”
Read the full article
Jones, G., McFarland, C., Lee, M., Reid, C., Rose, E., Gottlieb, J., & Falcon, I. (2024). Identifying and Developing the Battery Manufacturing Workforce: A Regional Analysis of Supply–Demand of Skilled Workers. Economic Development Quarterly, 0(0).