When people think about robotics today, they tend to think of hard and rigid metal structures driven by powerful motors. Many robots do in fact have hard structures (not to mention hard and rigid actuators, sensors and grippers), which can make them heavy, slow, inefficient, expensive, and potentially dangerous when it comes to working side by side with people.
But what if robots could emulate humans or other creatures in nature? What if they could harness the manual dexterity of humans, the maneuverability of birds, or even change their surface texture based on environmental context? Unlike traditional robots, nature offers hard and soft structures, actuators, sensors, and grippers that achieve many of these capabilities. Soft structures and systems are also inherently safer when interacting with people.
New Trend Toward “Soft” Robotics
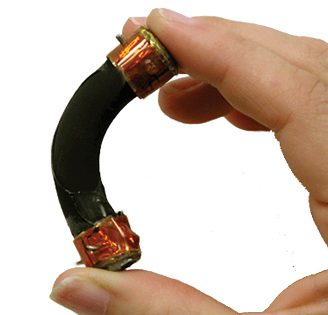
We are now seeing fundamental changes in the field where improvements in materials are literally re-shaping robotics. The new trend is moving towards “soft robotics,” driven by improved capabilities, lower costs, and increased safety for human interaction. The SRI Robotics Program is at the forefront of this movement, with innovative materials technologies that are changing the way many types of industrial, medical, consumer, automotive, and aerospace robots are powered and operated. Key SRI technologies at the heart of this evolution are electroactive polymers or “artificial muscles,” electroadhesion gripping, and electrolaminates. SRI’s patented smart material, “artificial muscle”, behaves much like a human muscle. It expands when exposed to an electric current is removed, converting electrical potential energy into mechanical motion.
Electroactive polymer artificial muscles expand when a voltage is applied and contract when the voltage is removed, thus converting electrical energy into mechanical motion. Unlike other voltage-controlled materials such as piezoelectrics, artificial muscles have the force and stroke of natural muscle. These characteristics can enable robots to mimic the dexterity and mobility of humans. In contrast, pneumatics—a technology that powers most of today’s soft robotics—requires noisy air compressors, hard-to-control valves and awkward hoses.
Another robotics trend enabled by electroactive polymers is the ability to change surface texture and even develop skins that can sense pressure and contact, which is particularly important as robots start to work side-by-side with humans. A driving force behind these new sensing developments is the need for wearable sensors that achieve comfort and function by matching skin impedance. Because these stretchable polymers can also act in reverse with low hysteresis, meaning that it can generate power by being stretched and contracted while achieving consistent results, they can also be built into clothing and fabrics to measure motions and forces. Commercial organizations are developing electroactive polymer materials based on SRI licensing for a diverse range of applications where soft, flexible, and electrically-active for actuation or sensing are important.
The market is also starting to see soft grippers with new capabilities. Unlike their rigid counterparts, soft grippers can pick up a wide variety of objects with minimal sensing and control. An extreme example is found with “jamming” grippers, in which a flexible sack is filled with a powder-like substance that can conform around an object of almost any shape. A vacuum process then makes the soft gripper rigid, enabling it to pick up the object through friction—without any intelligence or complex processing.
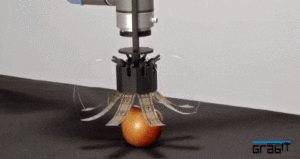
Grabit Inc.’s Each Pick prototype demonstrates the acquisition and
transfer of unwrapped products of various shapes, sizes and weights.
Electrostatic forces can be used to pick up and move objects that might be too delicate to squeeze with the forces needed to produce sufficient frictional forces. Similar to the principle of rubbing a balloon on hair to create electrostatic attraction, this soft and flexible technology allows for electrically controlled adhesion to grip almost any object.
GrabIt, Inc., an SRI spin-off company, provides a good example of this technology in action for materials handling. Using electroadhesion technology licensed from SRI, GrabIt’s robot hands can grip a wide variety of objects. Electroadhesion can also more securely transport objects moving along conveyer belts—resulting in a quicker, more flexible, and cost-effective option for many manufacturers and product distributors. The SRI Robotics team has applied this electroadhesion technology in wall-climbing robots that are effective on a range of surfaces—even damp or rough surfaces. These robots can be used for inspection, surveillance, as toys, or even eventually for cleaning hard-to-reach places in buildings.
And what if materials could change from soft to hard on-demand? SRI is working on electrolaminate technology that can enable a material to change from being pliable like rubber to rigid like steel—without adding significant bulk, mass, or power to the materials. These materials—types of metamaterials or mechanical materials—are built of repeating elements. Connections within the elements can be changed by electrostatically clamping different layers together. Compared to more traditional smart materials and systems, electrolaminates use only low-cost and lightweight flexible polymers, offer far greater stiffness variation and elongation (orders of magnitude vs. percent), and can react quickly. These characteristics result in lighter, cheaper, less complex structures that can absorb a great amount of energy. To date, we’ve demonstrated electrolaminate straps able to hold up to 150 pounds.
Perhaps one of the most compelling applications for this technology is human performance enhancement. In a Veterans Administration-funded effort, SRI’s electrolaminates are enabling MIT’s FitSocket technology to more effectively adapt to changing loads and limb volumes for prosthetic limbs. Inspired by the construction of a barrel with straps that hold it together, SRI has developed straps from electrolaminate materials that comprise the interface between prosthetic limbs and the human body. The straps become rigid when the limbs are in motion, and then soft and flexible when the limbs are at rest. For DARPA’s Warrior Web project, SRI’s electrolaminates are used to construct undergarments to work with the human body’s musculoskeletal system to absorb energy and then release it for reducing physical burden on military soldiers. Such materials can make robots interact more safely with humans by, for example, allowing the robot’s structure to become soft should a potential collision situation be detected.
These examples are just a few of the applications and capabilities that are possible because of advances in soft robotics, driven by the notion that robots can approach the capabilities of natural creatures. Not only can soft robotics provide options that are faster, stronger, and more dexterous than traditional hard robotics, they can be safer and more cost-effective. Of course, there still are many applications where rigid capabilities are required. But as humans and robots work together more closely, imagine that if a rigid robot came close to hitting a person it would sense that and either stop or even shape around the human part. With advancements in soft robotics, that time is not far away.