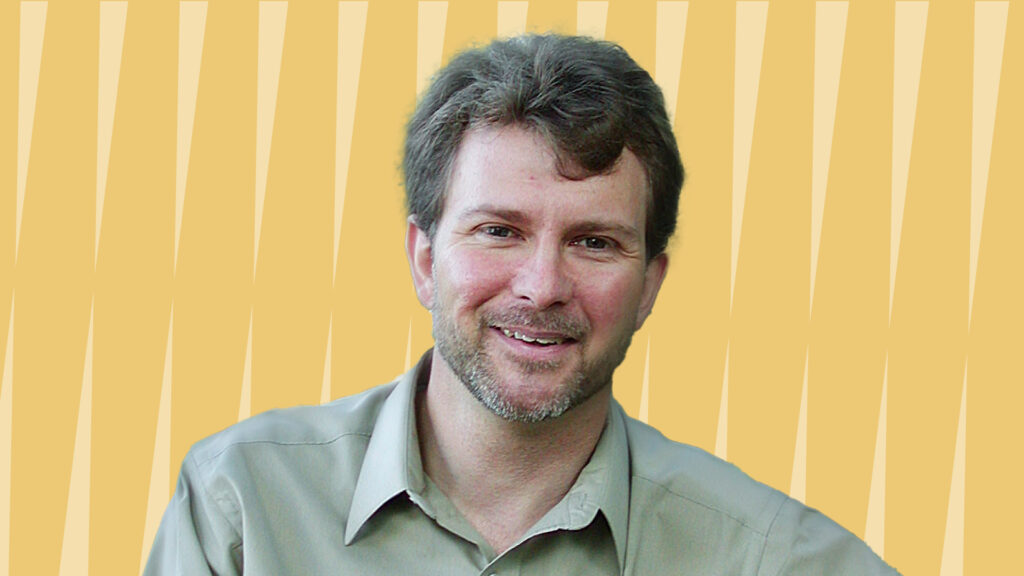
The director of SRI International’s Robotics Laboratory has built a career filled with breakthroughs and world-firsts
Thomas Low, director of SRI International’s world-renowned Robotics Laboratory, has been spearheading advancements in automation, machine learning and related fields for more than 35 years, but he still approaches his work with the energy and enthusiasm of an eager scientist just starting out.
Low doesn’t even think of it as work. For him, it’s a passion.
“This is what I do for fun,” Low says.
This passion that powers him has been essential to his long and successful career. He has been a driving force behind incredible advancements in robotics and holds 47 U.S. patents. At SRI, he has been a pioneer in telerobotics and led the creation of the first autonomous, motorcycle-riding, humanoid robot.
“There are a lot of exciting things to keep exploring,” Low says.
So, who is Thomas Low? What has he done? And what is he up to next?
Building on an SRI legacy
For Low, SRI is a bit of a family affair.
His father was a program director at SRI for more than 30 years. In 1984, after Low graduated from the University of California, Berkley, with a degree in mechanical engineering, he went straight to work at SRI. He began in a mechanical engineering lab. A few years after joining, SRI supported him in earning his master’s degree in mechanical engineering from Stanford University.
SRI was a great fit from the outset, and, like his father before him, Low has enjoyed a long and fruitful tenure at the nonprofit research organization. “I was put in with some fine people from the start and became part of a very strong team,” he recalls. “I was really lucky.”
During his career at SRI, Low has developed new robotic systems and technologies for commercial and government clients.
His work has taken him into fields beyond robotics, including software development, mechanical design, computer-aided engineering, manufacturability, electromechanical systems, sensor development, real-time computer graphics and dynamic simulation.
He has also led projects in automation and material handling, autonomous vehicles, advanced human-machine interfaces, medical devices and robotics, teleoperated robotic systems, drug delivery devices and plasma processing instruments.
During his early days at SRI, Low delved into medical devices and automation. Work on blood-pressure monitoring systems, for instance, led to the development of a medical device that was his first-ever FDA-approved product — a milestone for sure. “Medical became a big focus for us,” says Low.
Other projects from his prolific career range from inkjet and sublimation printing to innovations for the U.S. Postal Service. “We were creating these sorting and package handling systems,” explains Low. “For the time, it was very new, very difficult automation work.”
In the 1980s, Low recalls that robotics was “the new hot thing.” The possibilities in the emerging field stoked his scientific passions, and he was thrilled when his focus at SRI increasingly turned to automation and robotics. “It was exciting to be part of something that felt leading edge,” he says.
A pioneer in telerobotics
Exciting is indeed the word to describe many projects Low has worked on throughout his career.
For example, he was an essential member of the SRI team whose groundbreaking work pioneered minimally invasive telepresence surgery.
Low and the robotics team, aligned with Phil Green and his SRI Biomedical Research Laboratory created the first telerobotic surgical system approved by the U.S. FDA. Subsequently, Intuitive Surgical Inc. licensed the technology, and its DaVinci system is now the market leader in surgical robotics. Used throughout the U.S., Europe and Asia, the system’s robotic arms allow difficult surgical procedures to be performed laparoscopically, allowing patients to recover more quickly and with less pain and complications.
“With the kind of projects we do, it really requires you to be good at risk management,” Low says. “Some of the best engineers are the ones who are not afraid to take a risk, but they do so in an intelligent, well-planned way.”
Building on the DaVinci system’s landmark success, Low and the SRI robotics team created Taurus — a small, lightweight teleoperated robot system that provides remote precision and manipulation. Employing many of the innovations that enabled the success of DaVinci, the Taurus robotic system is used for applications that are hazardous or dangerous, allowing the operator to remain a safe distance away.
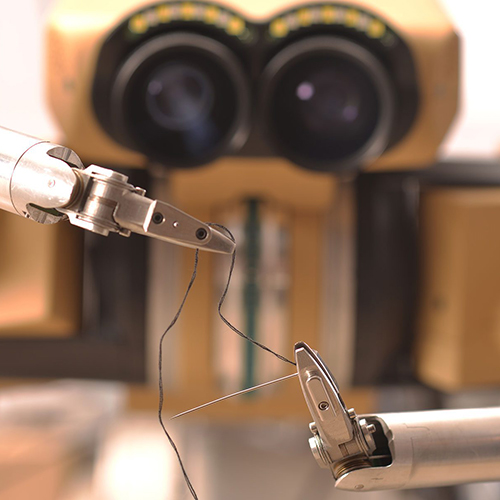
Taurus is used in extreme environments, for dangerous tasks such as defusing bombs and is being adapted for emergency field surgery. It has two independently controlled robot arms. Each of those has graspers and seven joints that replicate a human arm. Taurus also features a vision system that combines stereoscopic high-definition cameras and an immersive 3D display. All of this adds up to giving Taurus unparalleled fine-manipulation capabilities. Plus, it’s easy to use thanks to an intuitive interface that requires minimal training.
“People tend to think about the robot side and not really dwell on the user interface,” says Low, “but it’s the interface that decides whether what you built is going to work or not.”
From MOTOBOT to Fukushima to the moon
Low tallied another world’s first when he and his SRI robotics colleagues teamed up with Yamaha to create MOTOBOT. Never before had anyone built a humanoid robot that could independently ride an unmodified motorcycle, until MOTOBOT.
The impetus behind the project was to create a robot that could be used in precision testing experiments of high-performance motorcycles — an undertaking that helps engineers improve the performance of racing bikes but can be dangerous for human riders. With MOTOBOT, however, there’s no danger because a robot is doing the riding.
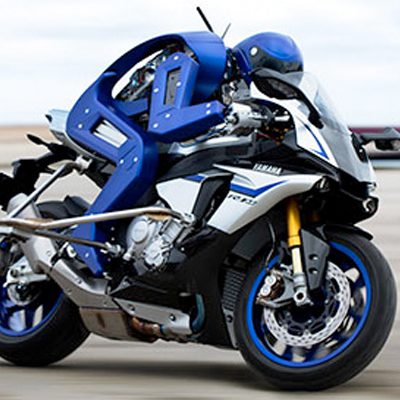
The implications of the rider robot go well beyond Yamaha’s motorcycle testing. The lessons learned as MOTOBOT becomes more precise and able to increasingly use machine learning are providing valuable insights for the entire field of autonomous vehicle design.
Some of Low’s projects have been intense pressure cookers, performed for high stakes. Long before the 2011 earthquake and tsunami in Japan caused the Fukushima Daiichi nuclear disaster — the worst atomic disaster since Chernobyl — Low and his team spent more than four months working around the clock to develop a robot that could operate in ultra-high radiation environments to make repairs in the Fukushima reactor containment vessel.
“From a pressure standpoint and a technical standpoint,” says Low, “it was almost an impossible job.”
Nonetheless, Low seems to make the impossible happen before most people have their morning cereal. And that’s just what he intends to keep doing.
Though he’s accomplished so much throughout his long career, he’s not about to rest on his laurels. He’s excited about new projects the robotics lab is engaged in, such as a collaboration with NASA. This project centers on creating an entirely new robot that can be used to do things like mine for water deposits on the moon. As a pilot and aviation enthusiast, the prospect of building a robot for space missions thrills Low, whose face lights up as he discusses the technical details before jumping to discuss other projects, eyes still illuminated with excitement.
“I love this stuff,” he says.